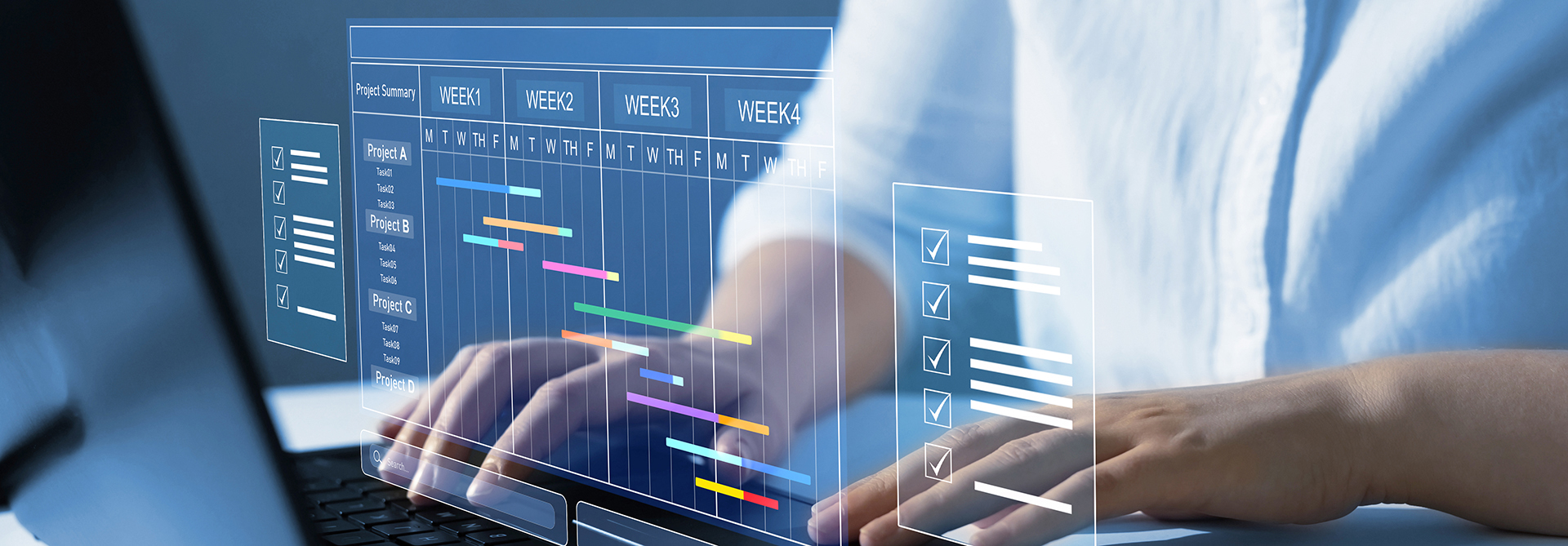
PROGRAM MANAGEMENT IN AUTOMOTIVE PRODUCTION: INTEGRATION OF DIFFERENT AREAS ACCORDING TO CUSTOMER REQUIREMENTS
Every production project has a beginning and an end point, and throughout its entire duration it is monitored and controlled by program management. A larger production order involves projects in different areas. If these are to be bundled, they are referred to as program management.
Depending on whether it is a solitary / first launch or split production, product development may also be involved in programs. In other cases, the production of a vehicle that has already undergone final development must be integrated into existing processes and infrastructure in the manufacturing location. The development, production and supply chain management departments, for example, are integrated into the individual programs, which combine all the main vehicle production processes.
In any case, and regardless of the exact definition of the projects, program management is defined as a bracket over product development, production integration and supply chain development.
PROGRAM MANAGEMENT STARTS WHEN THE REALIZATION OF A POTENTIAL BECOMES PROBABLE
The first point of contact with a prospective customer is usually arranged by the sales department. In the case of a new project, a quotation team is defined first, which determines important cornerstones of the project in advance.
The actual activities of program management begin as soon as a potential project is likely to move from the acquisition or offer phase to the realization phase. This is the point at which the project is commissioned and the focus shifts to drafting the contract and working out the technical implementation. The responsible program managers can handle the proposal at the same time and are therefore already involved in the previous offer negotiations with the customer.
This is an advantage for both customers and the manufacturing company because it ensures a consistent flow of information, and all parties have access to the requirements and objectives of the program.
This applies to both the content aspects, the timelines and commercial information. Program managers act as the central hub where all information converges. They are the main point of contact for the customer, i.e. the entity that will put the produced vehicle on the road. They know very well the challenges of the project in each of the various phases.
EARLY INVOLVEMENT OF MANAGERS FROM INDIVIDUAL DIVISIONS
The more detailed the project becomes, the more important it is to involve the managers of the individual departments. This guarantees that the customer experiences consistent partnership with the contract manufacturer. They interact with the same contacts from the outset and know who they can approach.
Everyone involved has the same status of information at every stage. The proposal team, and later, the program team are informed in detail about what has been negotiated with the customer and which critical issues require special attention.
DIFFERENT SCENARIOS FOR SENSIBLE OUTSOURCING OF PRODUCTION FOR VEHICLE MANUFACTURERS
In general, there are various reasons why a car manufacturer might outsource automotive production to a contract manufacturer. The most extensive case represents taking over the entire development, supply chain management and production as a general contractor.
Another option involves split production, where production volumes for certain markets are manufactured in close proximity to the targeted market, or covering production peaks that exceed the car manufacturer's own capacities. In addition, outsourcing the phase-out production of a vehicle type that is still in demand and is approaching the end of its product life can also be a sensible strategy. (Link: Automotive Production - Which Scenarios Favor Outsourcing to a Contract Manufacturer)
PRECISE PROCESSES AND METHODOLOGY FOR REALIZATION
The program management methodology follows a stage-gate process with precisely defines gates, milestones and corresponding deliverables. Along the milestone chain, a broad variety of activities are carried out simultaneously (product development, supply chain development and production process development) to maintain the timeline and minimize modification costs at later points in time. This is also known as simultaneous engineering.
In the case of a contract manufacturer, these processes and methodologies must be clearly defined. However, they must also provide the necessary flexibility to adapt and be synchronized with the respective customer.
INDIVIDUAL CASES, INDIVIDUAL PROGRAM OBJECTIVES
The automotive production business model is decisive for the point of entry of a contract manufacturer in a manufacturer's vehicle project. With the traditional model, it can be assumed that the concepts are already precisely defined. These manufacturers have their own internal processes, parts kits and platforms, and a very specific vision of the vehicle's appearance. The manufacturing partner usually receives a detailed specification sheet already clearly defining the vehicle and mapping out the objectives. This provides a clear catalog of goals that must be realized.
The contract manufacturer has the task of developing efficient solutions to produce the vehicle for the supply chain and production. The aim is to keep non-recurring cost costs to a minimum and reduce additional investments by using existing facilities and equipment while also developing optimized solutions for recurring costs. The entire business case must always remain in focus and is often developed together with the customer. After all, it is in the interest of the contract manufacturer that the finished vehicle is a market success and that the planned production volumes are achieved.
DETERMINING THE DEPTH OF ADDED VALUE IS ESSENTIAL
Depending on the individual case, the manufacturer determines in advance which suppliers are suitable for a project. For many assemblies, however, the manufacturing company can also decide which components to purchase as sub-assemblies or modules and which to manufacture or at least assemble in-house. For this purpose, the projected lifetime volume, i.e. the number of units over the lifetime of the program, must be considered.
Logistics is also an important aspect of a program. How do the parts get from the supplier to the plant as efficiently and reliably as possible? How do they get from the warehouse to the production line? The optimal compromise must be found to reduce the amount of capital stored in inventories while ensuring a high level of security in the event of supply chain disruptions. All strategies must be considered under the aspect of total cost of ownership for the overarching business case.
NEW ENTRANTS REQUIRE A DIFFERENT APPROACH TO DEFINING PROGRAM OBJECTIVES
In projects with new vehicle manufacturers, the contract manufacturer must join at a much earlier stage. In these cases, the first entry point is development. Depending on the individual case, a contract manufacturer such as Magna can take on the entire development of a vehicle type even if only rough key data is known, e.g., vehicle type, powertrain concept, intended target markets and market positioning.
Program management must first establish the objectives of the vehicle together with the potential manufacturer, including the technical objectives. These should be derived from the market conditions and the competitive environment in the targeted segment. The manufacturer should have a clear awareness of the desired unique selling propositions (USPs) of the vehicle in the market and define these together with the development partner.
Based on these initial definitions, it is then necessary to identify possible donor platforms and carry over parts from existing vehicles. This reduces costs and lead times for the customer. If development service providers and production partners work together, as is the case with Magna, it is easier to find the optimal and cost-efficient solution.
Of course, different program objectives can contradict each other, which is also referred to as a target conflict. Each role in the program tries to achieve its objectives, but it is the task of the program management to balance target conflicts and to achieve the best possible outcome.
SPECIFIC ADVANTAGES OF AN EXPERIENCED MULTI-OEM MANUFACTURER AS A PRODUCTION PARTNER
Due to the multitude of completed and ongoing production programs for a wide variety of vehicle manufacturers, a multi-OEM serial manufacturer such as Magna can rely on a great amount of experience on the one hand and on an existing global supplier network on the other. This facilitates the work of program management and thus shortens the preparation time. The manufacturer gains a competitive advantage because the new vehicle can enter the market sooner and non-recurring costs can be reduced.
In some cases, due to its in-depth expertise, professional program management can also show the manufacturer possible ways of cooperation while ensuring the protection of the product and the confidentiality of know-how. This way, the manufacturing partner can even become a link between different manufacturers and trigger synergies as neutral third party.
CUSTOMER PROXIMITY AND COST SAVINGS THROUGH GLOBAL ORGANIZATION
A manufacturing partner for automotive production with global presence has great advantages for the manufacturer. Regardless of the continent, there are always contacts available who are located within a reasonable distance and within the same time zone. This can not only help minimize travel costs, but it also facilitates online communication, thus speeding up processes and extending the time window for collaboration across several time zones.
This also results in cost advantages. Whether production takes place in the manufacturer's own plant or at a contract manufacturer, the most challenging phase of a vehicle project is always prior to the start of sales / Start of Production (SOP). During this period, funds are spent on planning work and equipment but no returns are generated yet. Investments start to be recovered after the Start of Production (SOP) and respective timing and cost reductions in prior activities can result in significant economic advantages.
EXISTING PRODUCTION INFRASTRUCTURE ACCELERATES THE START OF SERIAL PRODUCTION
For a new entrant that does not yet have their own
factories and production infrastructure, including the necessary supply chain,
outsourcing production to an experienced contract manufacturer offers
significant benefits from the very beginning. Building or acquiring a factory
not only requires high investments but also costs a lot of time until the
product can be launched on the market. Here too, professional program management
can find the best solution for both parties.
DATA EXCHANGE WITH INDUSTRY-STANDARD AND IN-HOUSE TOOLS
Program management also includes the IT aspect. Smooth data exchange between the manufacturer, the production plant and all relevant component and module suppliers is essential throughout the whole program – from planning start until end of production. This provides transparency in all areas and keeps all stakeholders on the same page. The contract manufacturer should therefore use industry-standard IT solutions but must also be able to adapt to respective custom solutions from partners.
If the manufacturer has not yet established the relevant systems (such as a new entrant), an all-round competent manufacturing partner will offer its own solutions to reliably map the required processes – from monitoring and controlling the material flow to the necessary and legally required documentation during vehicle production. This can also cut the time necessary before the vehicle can be produced and sold. The systems required during the program – for example for the exchange of design data, conversion of customer orders to production orders or management of the bill of material – are already determined during the quotation phase of each project.
STAYING FLEXIBLE IF THE PROJECT DEVELOPS DIFFERENTLY THAN PLANNED
No matter how careful the planning and preparation has been done, unforeseeable challenges will arise with every program.
Here, too, program management is required. Plans need to be rescheduled, and processes altered to prevent problems from happening in the first place. It is important to have as accurate a planning status as possible. In most cases, having a plan B to counteract certain risks is also helpful. Of course, this must be openly discussed with the customer beforehand. Nevertheless, a contract manufacturer should be willing and able to adapt flexibly to changing circumstances and new requirements.
FUTURE TRENDS IN THE AUTOMOTIVE INDUSTRY AND EFFECTS PRODUCTION PROGRAMS
After a phase of increasing segmentation, the trend in the automotive industry among recently established manufacturers seems to be towards reducing the complexity of manufacturers' model ranges. This considerably simplifies both production planning and production control.
This trend is supported by the concept of the software-defined vehicle. Functions and options are integrated into the vehicle by default on the hardware side, but are only made accessible to the end customer by activating them via software. This activation can also be temporary as part of a subscription model, reducing the number of variants on the production line. Phenomena that were common a few years ago, specifically that only a few out of 100,000 vehicles produced were truly identical, will hardly occur in future.
This simplifies the work in programs, as well as the trend towards more and more cooperation between different manufacturers in development. If several vehicles share a co-developed platform, it is easier for a multi-OEM manufacturer like Magna to bundle volumes from different customers and to balance them. Therefore, this possibility must be taken into account in modern program management.
Furthermore, the use of artificial intelligence for planning automotive production has just started. The increasingly wide-ranging possibilities offered by artificial intelligence (AI) are opening new perspectives for the virtual validation of production processes, simulation in development or detail planning of production execution along the supply chain. This enables production development to be simplified and shortened which can support the general trend towards faster and more cost-effective processes.
Stay connected with Inside Automotive!
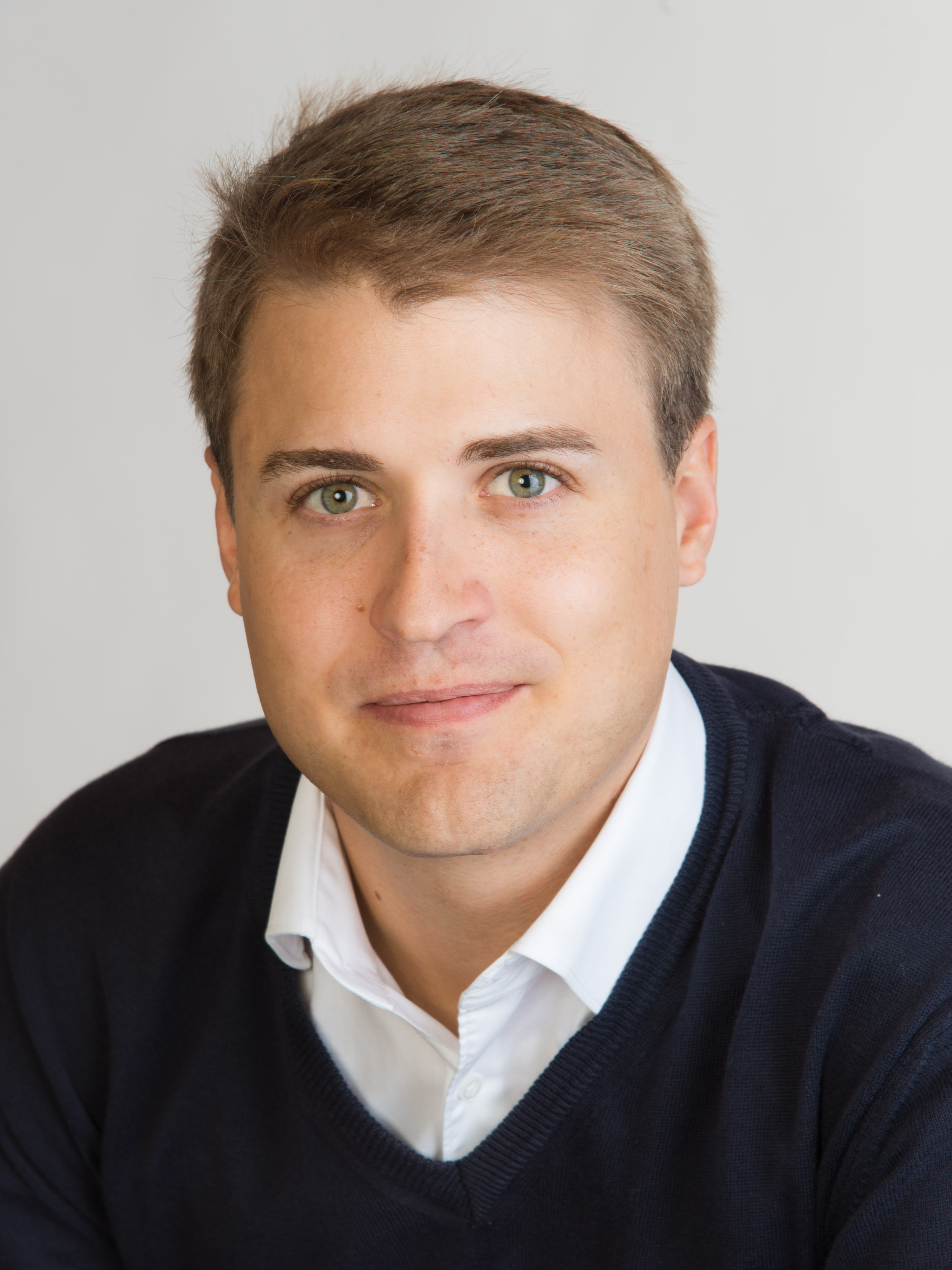
We want to hear from you
Send us your questions, thoughts and inquiries or engage in the conversation on social media.
Related Stories
Test First, Then Enter the European Market: Professional Battery Testing Examines More Than Just the Charging Curve
Blog
Quality Assurance at a Contract Manufacturer for Serial Production in the Automotive Industry
Blog
Stay connected
You can stay connected with Magna News and Stories through email alerts sent to your inbox in real time.